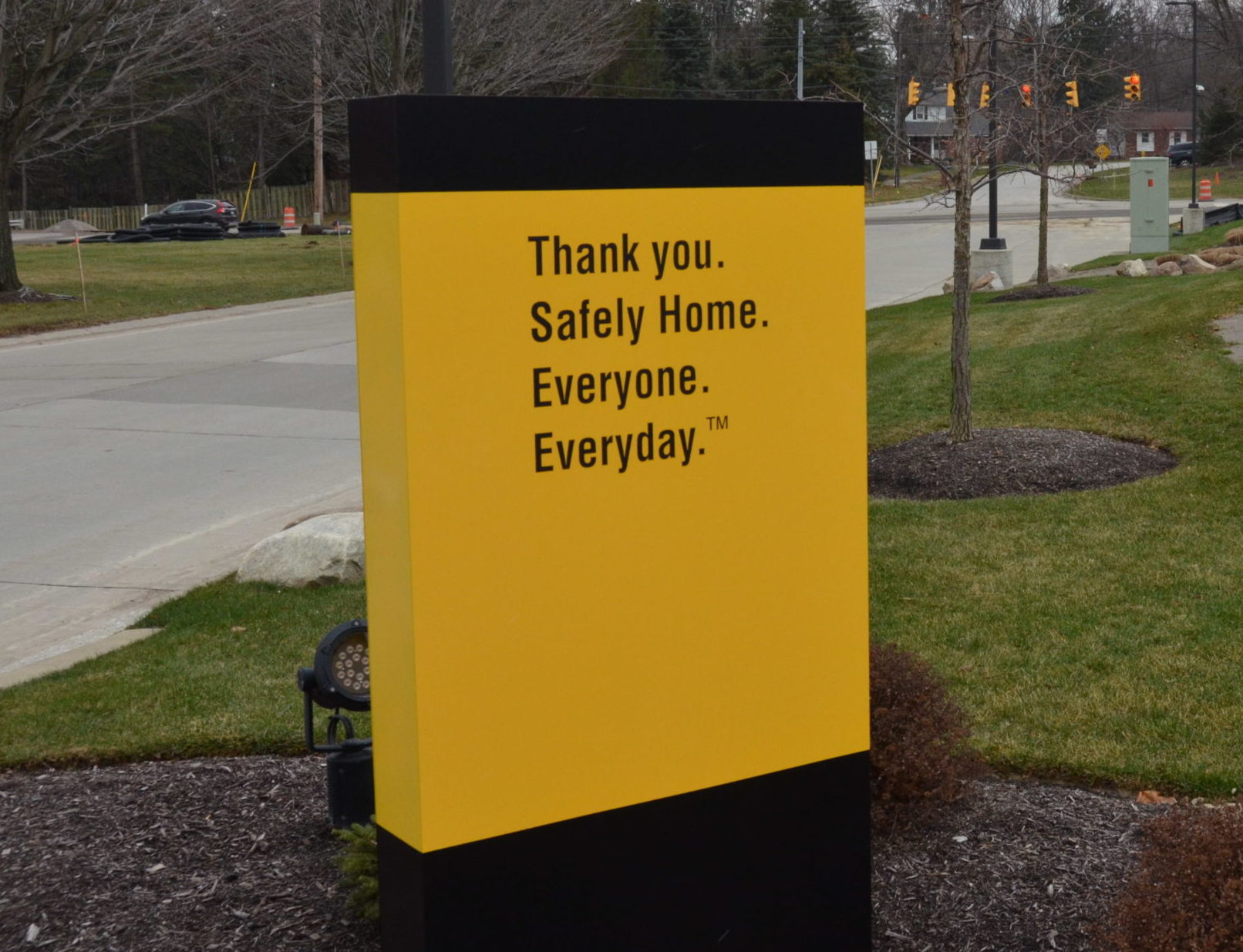
Note: This is a contributor post from Monti Zimmerman, Safety & Environmental Manager, Ohio CAT
Working within an industry that promotes a strong safety culture is fundamental to ensuring that all employees return home safely every day. Employee safety and wellbeing is a foundational value within the construction industry that allows businesses to operate safely while supporting quality production.
To determine the effectiveness of safety programs, traditionally lagging safety indicators such as Total Recordable Incident Rates (TRIR) or Lost Time Incident Frequency (LTIF) rates were used to measure the success of safety by looking at the number of injuries that occurred within an organization or industry as a whole. While such lagging indicators are still common today, Safety Professionals have realized for some time that the more effective trend in safety management is to develop qualitative leading indicators that can be used to identify and mitigate risk and can be a predictive analytical tool that allows safety and operational professionals the ability to focus resources where needed. In essence, instead of looking at just past performance (injuries), leading indicators focus on behaviors, activities, and the overall safety culture that supports injury prevention.
The National Safety Council’s Campbell Institute provides the following leading indicator definition:
“Proactive, preventative, and predictive measures that monitor and provide current information about the effective performance, activities, and processes of an EHS management system that can drive the identification and elimination or control of risks in the workplace that can cause incidents and injuries.”
To demonstrate how industry has implemented this forward looking measurement system, let’s review Ohio Machinery Co. dba Ohio CAT’s leading indicator system. Ohio CAT has established a comprehensive safety system that emphasizes Accountability, Commitment and Involvement. A key component of this is accomplished through an internal leading indicator safety performance measurement system, which is called SAFEWorks (Safety Activities For Employee Wellbeing).
Similar to many organizations, Ohio CAT does track traditional safety measurements such as TRIR rates and LTIF rates, however the SAFEWorks model places an emphasis on the behaviors, systems and operational processes that drive those rates. While there are many leading indicators that can be used, the SAFEWorks performance measurement indices at Ohio CAT are as follows: Comprehensive Safety Audits (Processes/Activities/Behaviors); Safety Observations (Behaviors); Operations Management/Supervision Safety Inspections (Behaviors/Processes); Safety Training Participation; Safety Committee Meetings; and Toolbox Talks. Each component of the SAFEWorks system is weighted and quantitatively aggregated to provide an overall performance measurement score, which is evaluated at a macro (Corporate/Divisional) and micro (Individual branch location) levels. Providing a score allows executives and safety/operational professionals the ability to evaluate the overall performance of a given area and identify potential gaps and future risks that may arise based on the adherence and performance related to the leading indicators. In Ohio CAT’s case, there is tangible evidence that shows those business segments that meet their leading indicator goals have lower injury rates.
Organizations throughout industry have been adopting similar approaches in an attempt to eliminate injuries, reduce organizational risk and maintain business continuity. The maturity of an organization’s safety culture will help in determining the types of leading indicator measurements that are most effective for each individual organization. While those indicators can vary by organization, the key is implementing a system that works for the current safety culture. Being proactive in safety within our industry is fundamental in preventing injuries and ensuring: Safely Home. Everyone. Everyday. ™